Action plan
Where it cannot be demonstrated that exposures do not exceed an exposure limit value, it is a requirement under regulation 7 of the Control of EMF at Work Regulations 2016 to make and implement a suitable and sufficient action plan to ensure exposures do comply. Note that this requirement does not apply where field strengths exceed only one or more action levels.
This Appendix is a modification of that found in the Control of EMF at Work Regulations, 2016, to address static magnetic fields.
Where relevant, the action plan should include consideration of:
- alternative working methods involving lower exposure
- replacement equipment producing lower exposures
- technical measures to reduce emissions of electromagnetic fields, including interlocks, screening or similar protection measures
- demarcation and access control
- maintenance programmes for equipment, workstations and workplaces
- design and layout of workstations and workplaces
- limitations on the duration and intensity of exposure
- availability of suitable personal protective equipment
The purpose of the action plan is to achieve compliance with the exposure limit values, so whenever there is evidence that the exposure limit values have been exceeded, employers are required to identify and implement whatever changes are needed to reduce exposures below the exposure limit values.
Where an action plan is required, the employer must keep a written record of the most recent plan.
Risk management
It is a requirement to implement measures to either eliminate risks identified by an EMF-specific risk assessment or reduce them to a minimum. The approach taken should follow the principles established by the Management of Health and Safety at Work Regulations 1999. In particular, employers are required to consider:
- technical progress
- potential to restrict access to parts of the workplace
- availability of measures to control the production of electromagnetic fields at source
The practical application of these principles should lead to consideration of a number of control. These are presented below:
- It must be ensured as far as reasonably practicable that where equipment likely to generate a strong static magnetic field is purchased or borrowed, that the supplier provides details of the likely field characteristics and recommended control measures. Such data should already be provided if the equipment is ‘CE’ or ‘UKCA’ marked and falls within scope of the Supply of Machinery (Safety) Regulations 2008, but nevertheless it is recommended that the equipment is re-tested locally to confirm the accessible field strength.
- Equipment generating strong static magnetic fields should be positioned as far away as reasonably practicable from areas normally occupied by staff and others.
- Ferromagnetic objects should be excluded from the vicinity of equipment generating strong static magnetic fields.
- Consideration should be given to the installation of shielding (normally either passive steel shielding for large areas or active systems to reduce fields at source) where there are significant stray fields that could present a risk to people.
- Work to assemble equipment incorporating strong permanent magnets should be carefully planned and executed using appropriate jigs to restrict the movement of magnets.
- Equipment designed and constructed in-house must be surveyed as part of the commissioning process.
- Managers responsible for new equipment generating strong static magnetic fields should ask the relevant MPA to undertake a field survey during commissioning.
- Warning signs as shown below indicating the presence of strong fields should be posted as appropriate where exposure above action levels may occur. Warning signs can be obtained from the SHE Group.
Signs required where the action level for interference with active medical devices is exceeded.
| 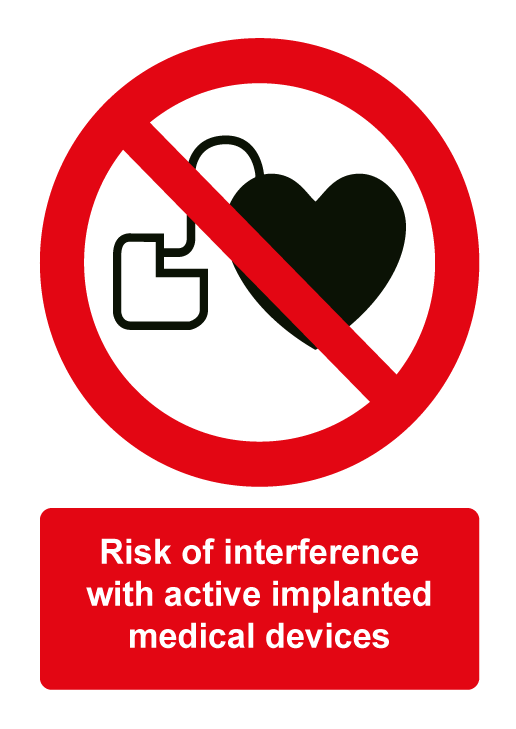
|
Signs required where action level for projectile risk is exceeded